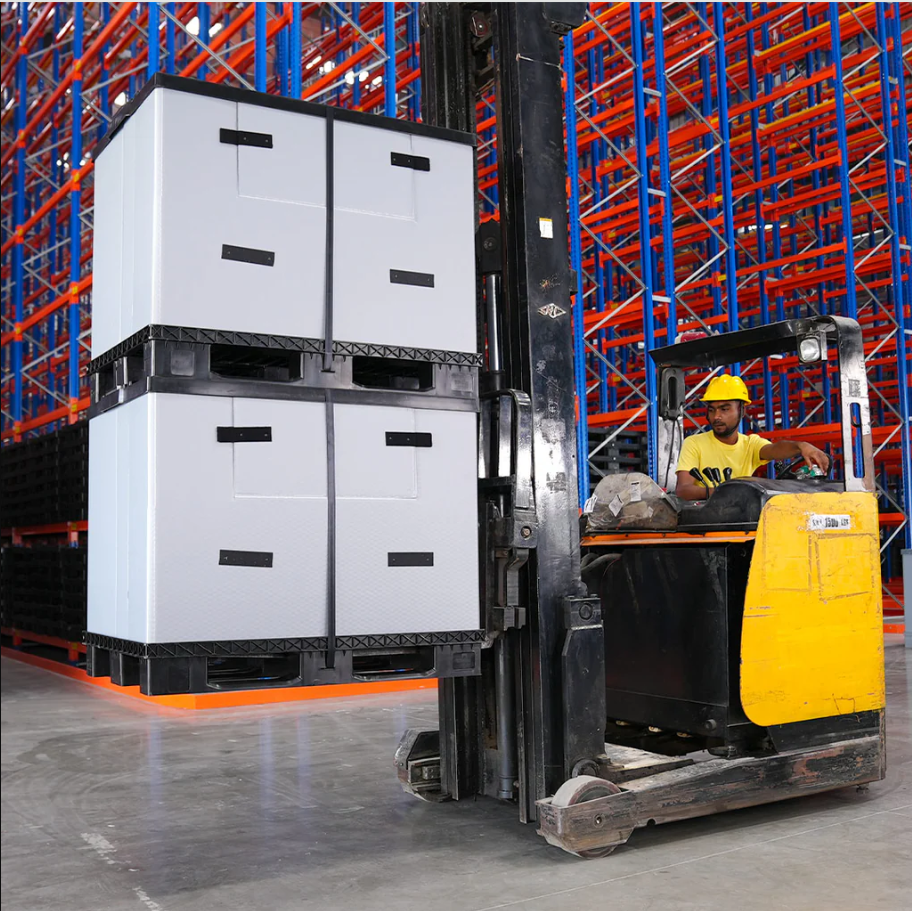
In the fast-paced world of automotive manufacturing, efficiency is paramount. With supply chains stretching across the globe and countless components involved in vehicle production, packaging plays a vital, often underappreciated, role. From tiny electronic sensors to heavy metal parts, every item needs to arrive safely, intact, and ready for assembly. This is where automotive packaging solutions come into play.
Automotive packaging isn’t just about boxes or containers. It’s a carefully engineered system that supports lean manufacturing, ensures product integrity, reduces waste, and improves sustainability across the value chain. Let’s explore what makes automotive packaging unique, what kinds of solutions are commonly used, and how the industry is evolving to meet new challenges.
The Unique Challenges of Automotive Packaging
Unlike standard commercial packaging, automotive packaging deals with complex, often fragile or oddly shaped components. Consider the range of items involved: engines, exhaust systems, dashboards, brake systems, wiring harnesses, and even glass panels. Each has its own set of protection needs.
Here are some challenges that drive the need for specialized automotive packaging solutions:
Component diversity: Automotive parts come in varying sizes, materials, and fragility levels.
Global logistics: Parts are often shipped over long distances in varying climates.
Just-in-time manufacturing: Delays or damaged components can halt production lines.
Sustainability pressures: The industry is under increasing scrutiny to reduce waste and improve environmental responsibility.
Addressing these challenges requires not only physical protection but also systems that optimize space, handling, and reusability.
Types of Automotive Packaging Solutions
1. Returnable Packaging Systems
Returnable or reusable packaging is a major trend in automotive logistics. These are custom-designed containers that can be sent back and forth between suppliers and manufacturers multiple times. They reduce waste, lower total packaging costs over time, and often feature collapsible designs for return shipment efficiency.
Returnable packaging often includes:
Foldable large containers (FLCs)
Dunnage systems (internal protective inserts)
Reusable crates and totes
Pallet sleeves and custom racks
2. Dunnage Solutions
Dunnage refers to the custom inserts placed inside packaging to secure parts. This can be made from foam, plastic, fabric, or other materials, depending on the part's protection needs. Dunnage systems are especially important for delicate items like electronic sensors, painted surfaces, or precision components.
The right dunnage helps:
Prevent scratches, dents, and movement during transit
Organize components for quick line-side access
Maximize space inside reusable containers
3. Bulk and Heavy-Duty Packaging
Large or heavy parts such as engines, transmission systems, or axle assemblies require rugged packaging solutions. These may involve reinforced pallets, metal racks, or custom wood-based structures that can handle the weight and provide secure transport.
These solutions often integrate:
Shock absorption materials
Corrosion-resistant coatings
Load-bearing reinforcements
RFID tagging for traceability
4. ESD (Electrostatic Discharge) Packaging
Automotive electronics are growing rapidly with the advent of electric vehicles and smart features. Components like ECUs (electronic control units), infotainment systems, and sensors require ESD-safe packaging to prevent damage from static electricity during handling and transport.
5. Protective Packaging for Export
When parts are shipped internationally, especially by sea, long transit times and exposure to humidity or rough handling require extra precautions. VCI (vapor corrosion inhibitor) films, moisture barrier bags, and reinforced outer packaging are common solutions used to ensure safe overseas shipment.
Benefits of Well-Designed Automotive Packaging
Implementing optimized automotive packaging solutions has a measurable impact on overall operations. Some of the key benefits include:
1. Improved Supply Chain Efficiency
Packaging that’s easy to stack, move, and store increases efficiency in warehouses and reduces loading and unloading times.
2. Damage Reduction
Custom inserts, sturdy materials, and secure closures minimize the risk of damaged goods, which helps reduce downtime and costs associated with replacements or returns.
3. Sustainability and Waste Reduction
Reusable packaging significantly reduces single-use plastic and cardboard waste. Many automakers now track their packaging footprint as part of sustainability goals.
4. Cost Savings Over Time
While reusable systems may have a higher upfront cost, they offer a better return on investment through repeated use, lower damage rates, and reduced disposal needs.
Trends Shaping the Future of Automotive Packaging
The automotive industry is in flux, and packaging must evolve accordingly. Here are a few trends shaping the future:
1. Digital Integration
Smart packaging systems with RFID tags or QR codes are helping track shipments, manage inventory, and support real-time logistics planning.
2. Customization at Scale
OEMs and Tier 1 suppliers are seeking modular packaging designs that can be customized for specific models or components without the need to design from scratch every time.
3. Sustainable Materials
There’s a growing shift towards recyclable plastics, biodegradable liners, and packaging designs that reduce carbon emissions across their lifecycle.
4. EV Component Packaging
Electric vehicles come with new components—like lithium-ion batteries, cooling systems, and high-voltage parts—which require specialized, often regulated, packaging solutions to ensure safety and compliance.
Conclusion
As the automotive sector embraces innovation, sustainability, and digitalization, automotive packaging solutions are becoming increasingly integral—not just for logistics but for overall operational success. From protecting complex components to supporting global just-in-time manufacturing systems, these packaging systems ensure that vehicles are built with precision, safety, and efficiency.
Manufacturers and suppliers who invest in the right packaging strategies stand to gain in terms of reduced waste, better quality control, and enhanced supply chain resilience. As vehicles continue to evolve, so too must the packaging that supports their journey—from factory to finished product.
Write a comment ...